Das Plasmaschneiden ist ein thermisches Trennverfahren für elektrisch leitfähige Metalle. Es setzt auf einen heißen und mit hoher Geschwindigkeit auf das Werkstück treffenden Plasmastrahl, der das zu bearbeitende Material schmelzt und ausbläst. Infrage kommt das Plasmaschneiden dabei vor allem dann, wenn sich Werkstücke nicht brennschneiden lassen – also beispielsweise bei hochlegierten Stählen, Aluminium oder Edelstahl. Was das Verfahren auszeichnet, wie es im Detail funktioniert und welche Gase zum Plasmaschneiden nötig sind, erklärt gasido.de im folgenden Beitrag.
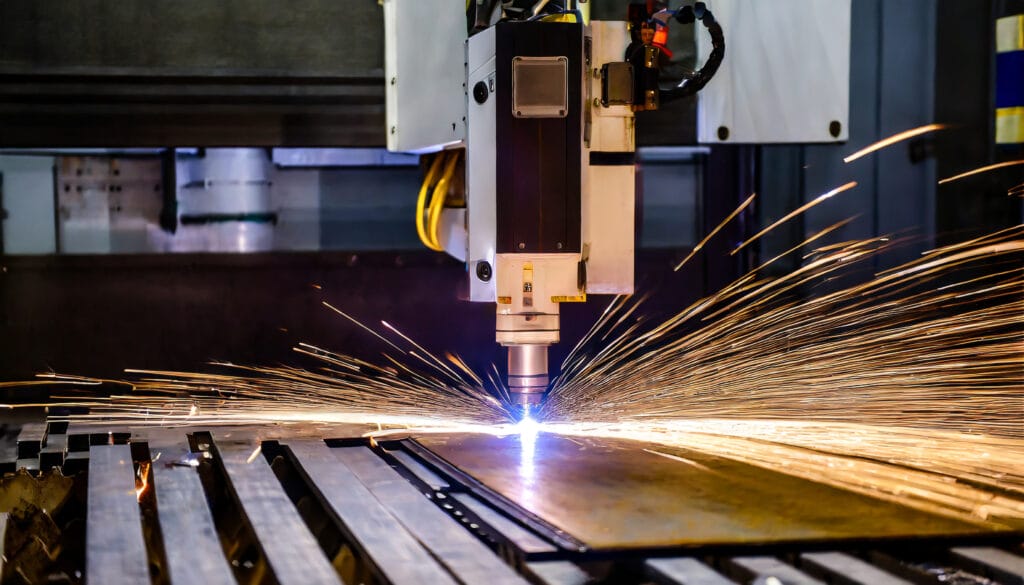
Themen im Überblick
Funktionsweise des Plasmaschneidens einfach erklärt
Ein elektrisch leitfähiges Material und ein beschleunigter Strahl aus heißem Plasma: Ist beides vorhanden, lassen sich Werkstücke schnell und vergleichsweise sauber trennen. Möglich ist das mit dem sogenannten Plasmaschneiden, das sich grundsätzlich von anderen Trennverfahren unterscheidet. Während beim Brennschneiden Sauerstoff das erhitzte Material oxidiert (verbrennt), findet beim Plasmaschneiden primär keine chemische Reaktion mit dem Werkstoff statt. Hier wird das Material direkt geschmolzen und aus der Schnittfuge geblasen, was einen großen Einsatzbereich sowie eine schnelle und saubere Metallbearbeitung ermöglicht.
Übrigens:
Das Plasma ist ein Gas, bei dem Elektronen aus der Atomhülle herausgelöst wurden (ionisiertes Gas). Die sogenannten Ionen liegen dadurch getrennt von freien Elektronen und neutralen Teilchen vor. Sie befinden sich in ständiger Wechselwirkung und sorgen dafür, dass das Gas elektrisch leitfähig ist. Dieser Umstand lässt sich beim Plasmaschneiden ausnutzen.
30.000 Grad Celsius heißer Plasmastrahl schmelzt Werkstoffe sofort
Beim Plasmaschneiden bringen Geräte einen Plasmastrahl mithilfe elektrischer Energie auf bis zu 30.000 Grad Celsius. Er trifft beschleunigt durch eine Düse auf das Werkstück und rekombiniert sich. Die bei der Ionisation herausgelösten Elektronen verbinden sich dabei wieder mit den Ionen und übertragen Wärme punktgenau auf das Werkstück. Dieses schmilzt sofort. Es wird vom Gasstrahl ausgeblasen und eine saubere Schnittkante entsteht.
Im Detail: Der Prozess des Plasmaschneidens Schritt für Schritt
Damit sich das Grundprinzip des Plasmaschneidens praktisch nutzen lässt, ist ein geschlossener Stromkreis zwischen Werkstück und Schneidgerät nötig. Dieser entsteht zwischen einer Elektrode im Plasmaschneider und einer Klemme an der Anode (dem Werkstück). Soll der Prozess starten, strömt ein ionisiertes Gas zwischen der Düse und dem zu bearbeitenden Metall. Berührt der energiearme Pilotlichtbogen das Werkstück, schaltet sich das Schneidgas zu und der energiereiche Hauptlichtbogen entsteht. Alternativ zu Schneidbrennern mit berührungsloser Pilotzündung gibt es auch Geräte mit Kontaktzündung. Wie der Name bereits vermuten lässt, muss der Brenner das Werkstück hier zunächst berühren, bevor der Lichtbogen zündet.
Wichtig zu wissen:
Elektroden sowie Düsen unterliegen dem Verschleiß und sind gelegentlich auszutauschen. Welche Elektroden beim Plasmaschneiden zum Einsatz kommen, hängt dabei vom Schneidgas ab. Während sich Wolfram für inerte Gase eignet, kommen bei reinem Sauerstoff und sauerstoffhaltigen Plasmagasen Zirconium oder Hafniumelektroden zum Einsatz.
Voraussetzungen und Einsatzbereiche in der Übersicht
Damit sich ein Material plasmaschneiden lässt, muss es elektrisch leitfähig sein. Das ist wichtig, da das Werkstück selbst ein Teil des Stromkreises ist und anders kein Lichtbogen zustande kommen würde. Da nahezu alle Metalle diese Voraussetzung erfüllen, ist das thermische Trennverfahren universell einsetzbar. So eignet es sich beispielsweise für dünne und mitteldicke Bleche aus:
- unlegierten Stählen
- legierten Stählen (auch CrNi- oder Edelstahl)
- Aluminium
- Messing
- Kupfer
und anderen leitfähigen Metallen. Im Allgemeinen lässt sich sagen, dass das Plasmaschneiden immer dann zum Einsatz kommt, wenn Werkstoffe nicht brennschneidbar sind.
Praktische Einsatzgebiete finden sich in nahezu allen Bereichen
Ob Hobby- oder Fachwerkstatt: Das Plasmaschneiden kommt heute in verschiedensten Bereichen zum Einsatz. So etwa bei der Fahrzeugtechnik, der Instandhaltung von Fabriken oder in Schweißreparatur- sowie Metallservicezentren. Aber auch auf der Baustelle und im Kunsthandwerk setzen Anwender auf das universelle Verfahren.
Übrigens:
Während in Werkstätten und kleineren Betrieben meist manuell bedienbare Plasmaschneider zum Einsatz kommen, nutzen Industriebetriebe häufig mechanisierte. Diese lassen sich automatisiert betreiben, um Bleche beispielsweise auf stationären Schneidtischen zu bearbeiten.
Vor- und Nachteile beim Plasmaschneiden von Metallen
Einer der größten Vorteile des Plasmaschneidens ist, dass sich damit alle elektrisch leitfähigen Materialien bearbeiten lassen. Das gilt sogar für hochlegierte Stahl- und Aluminiumwerkstoffe, bei denen herkömmliche Brennschneider an ihre Grenze kommen. Da der Wärmeeintrag in das Material lokal begrenzt und insgesamt eher gering ist, verziehen sich Werkstücke kaum. Darüber hinaus sind folgende Vorteile zu nennen:
- ausgezeichnete Leistung in vielen Bereichen dünner und mittlerer Blechstärken
- hohe Schnittgeschwindigkeit (10-mal schneller als Brennschneiden)
- Plasmaschneiden unter Wasser (großer Einsatzbereich, geringe Wärmeeinwirkung und Lärmschutz am Arbeitsplatz)
Nachteilig sind hingegen die Einsatzgrenzen, wenn es um die Stärke der zu bearbeitenden Bleche geht (120 bis 180 mm je nach Schnitt). Die Schnittfuge ist vergleichsweise breit und Plasmaschneider verbrauchen sehr viel Strom. Vor allem letzteres führt dazu, dass das Verfahren meist teurer als das Autogen-/Brennschneiden ist.
Plasmaschneiden im Detail: Verschiedene Arbeitsweisen
Abhängig vom Aufbau des Schneidbrenners lassen sich heute verschiedene Verfahrens- und Arbeitsweisen voneinander unterscheiden. Neben dem standardmäßigen Plasmaschneiden ohne Sekundärmedium führt die DIN 2310-6 dabei unter anderem auch die folgenden auf:
- Plasmaschneiden mit Sekundärmedium: Hier schafft man mit einem zusätzlichen Medium (zum Beispiel Wasser als Sprühnebel) eine bestimmte Atmosphäre im Bereich des Lichtbogens. Das schnürt diesen zusätzlich ein und reduziert die typische V-Form der Schnittfuge. Vorteil ist eine verbesserte Schnittqualität bei höherer Arbeitsgeschwindigkeit.
- Plasmaschneiden mit Wasserinjektion: Bei dieser Verfahrensweise bringen Plasmaschneider Wasser im Bereich der Düse ein. Dieses kühlt die Düse, bevor es sich als feiner Nebel um den Lichtbogen legt, um diesen einzuschnüren. Ein Teil des Wassers tritt zudem flüssig aus. Es kühlt das Werkstück, verhindert den Verzug und wirkt der Oxidation an der Schnittkante entgegen. Nachteil ist, dass nur eine der beiden Schnittflanken hohe Qualitätsanforderungen erfüllt.
- Plasmaschneiden mit erhöhter Einschnürwirkung: Hier sorgen hoch entwickelte Düsensysteme für die gewünschte Einschnürung des Lichtbogens. Das Präzisions-Plasmaschneidverfahren hat sich vor allem in der Industrie etabliert, da es bei hoher Bearbeitungsgeschwindigkeit für eine hohe Qualität sorgt.
Das Ziel der unterschiedlichen Verfahrenstechniken beim Plasmaschneiden ist es, den Lichtbogen enger einzuschnüren. Denn das ermöglicht das Erreichen hoher Qualitätsanforderungen bei hohen Schnittgeschwindigkeiten. Es sorgt in der Regel aber auch für steigende Kosten, wenn es um die Anschaffung von Maschinen und Anlagen geht.
Unser Tipp:
Für eine hohe Schnittqualität kommt es nicht nur auf den Plasmaschneider an. Auch die Schnittführung spielt dabei eine wichtige Rolle. Achten Sie dabei darauf, dass:
- Innenausschnitte zuerst geschnitten werden
- der Abfall beim Brennschneiden immer abwandern kann
- auszuschneidende Bauteile möglichst lange an der Grundplatte hängen
Halten Sie sich an diese Vorgaben, verhindern Sie weitestgehend, dass sich das Werkstück merklich verzieht.
Zum Plasmaschneiden benötigte Gase und Arbeitsmedien
Wer elektrisch leitfähige Materialien mit einem Plasmaschneider trennen möchte, benötigt neben dem Schneidbrenner selbst auch verschiedene Arbeitsmedien. Wichtig sind dabei vor allem die Plasmagase, zu denen Zünd-, Schneid- und Sekundärgase gehören. Zündgase sind nötig, um den Pilotlichtbogen auszubilden und den Zündvorgang zu erleichtern (Alternative: Kontakt-Plasmaschneider ohne Pilotzünder). Bei Schneidgasen handelt es sich um die eigentlichen Arbeitsgase und bei Sekundärmedien um Stoffe (Gase oder Flüssigkeiten), die den Plasmastrahl einschnüren und die Düse kühlen.
Arbeitsgase für Plasmaschneidgeräte beeinflussen die Schneidqualität
Während die Auswahl der Zünd- und Sekundärgase vom Schneidgerät abhängt (Herstellerangaben beachten), sind Arbeitsgase immer erforderlich. Welche zum Einsatz kommen, hat dabei einen großen Einfluss auf die Schnittgeschwindigkeit und -qualität. Die folgende Tabelle gibt einen Überblick.
Gase zum Plasmaschneiden | Eigenschaften |
---|---|
Druckluft | Das Gemisch aus Stickstoff und Sauerstoff eignet sich bei unlegiertem und legiertem Stahl sowie Aluminium. Nachteilig sind die Oxidation und die Bildung von Nitriden, die eine Nachbearbeitung erforderlich macht. Zudem oxidiert die Elektrode schneller, was höhere Verbrauchskosten nach sich zieht. |
Stickstoff (N) | Stickstoff eignet sich vor allem für rostfreien Stahl und Nichteisen-Metalle. Er ist günstig und reduziert den Verschleiß der Elektrode. Nachteilig sind aber auch hier die Nitrid-Ablagerungen. |
Sauerstoff (O2) | Sauerstoff eignet sich vor allem bei unlegiertem Stahl. Es ist günstig und ermöglicht eine hohe Arbeitsgeschwindigkeit. Die Schnittkanten sind dafür nicht optimal (eher etwas rau). |
Argon (Ar) | Argon reagiert nicht mit dem Werkstück und eignet sich daher zum Zünden sowie zum Austreiben der Schmelze. Es hat jedoch eine schlechte Wärmeleitfähigkeit und einen geringen Wärmeinhalt, wodurch es nicht als Einzelgas infrage kommt. |
Wasserstoff (H2) | Wasserstoff schnürt den Lichtbogen ein und sorgt auf diese Weise für eine bessere Schnittqualität. Außerdem ermöglicht seine reduzierende Wirkung die Bildung blanker (oxidfreier) Schnittkanten. Ausreichend sind dabei schon geringe Anteile. Als Einzelgas kommt es jedoch nicht infrage, da das Gas die Schmelze nicht ausblasen kann. |
Argon-Wasserstoff-Gemisch | Argon-Wasserstoff-Gemische sind für legierten Stahl und Aluminium geeignet (auch bei staken Blechen). |
Stickstoff-Wasserstoff-Gemisch | Das Gemisch kommt hauptsächlich für hochlegierte Stähle und Aluminium oder als Sekundärgas zum Einsatz. |
Gas zum Plasmaschneiden passend zum Material auswählen
Sie wollen Plasmaschneiden und sind unsicher, welche Gase für den jeweiligen Einsatzfall geeignet sind? Die folgende Tabelle hilft bei der Auswahl.
Material und Stärke | Gas zum Plasmaschneiden | Sekundärgas |
---|---|---|
Un- und niedriglegierter Stahl (0,5 – 80 mm) | Sauerstoff | Sauerstoff-Druckluft-Gemisch |
Un- und niedriglegierter Stahl (80 – 160 mm) | Argon-Wasserstoff-Gemisch | Stickstoff |
Hochlegierter CrNi-Stahl (1,0 – 6,0 mm) | Stickstoff oder Stickstoff-Wasserstoff-Gemisch | Stickstoff |
Hochlegierter CrNi-Stahl (5,0 – 160 mm) | Argon-Wasserstoff-Stickstoff-Gemisch oder Argon-Wasserstoff-Gemisch | Stickstoff oder Stickstoff-Wasserstoff-Gemisch |
Aluminium (1,0 – 6,0 mm) | Druckluft | Stickstoff oder Stickstoff-Wasserstoff-Gemisch |
Aluminium (5,0 – 160 mm) | Argon-Wasserstoff-Stickstoff-Gemisch oder Argon-Wasserstoff-Gemisch | Stickstoff oder Stickstoff-Wasserstoff-Gemisch |
Wichtig zu wissen ist, dass es neben der Gaszusammensetzung auch auf den Gasdruck ankommt. Dieser ist exakt einzustellen, um eine hohe Schnittqualität zu erreichen. Entsprechende Vorgaben finden Sie dabei in der Regel in den Produktunterlagen der Plasmaschneider.
Arbeitsschutz: Richtige Schutzausrichtung ist unverzichtbar
Das Plasmaschneiden ist ein thermisches Trennverfahren, von dem eine Reihe von Gefahren ausgehen. Dazu gehören unter anderem Schadstoffe wie Schneidstaub, Eisen- sowie Nickeloxide oder Ozon in der Atmosphäre des Arbeitsbereichs. Hinzu kommen glühende Funken und der hell leuchtende Lichtbogen, der ungeschützten Augen schaden kann. Zu den größten Gefahren zählen damit im Allgemeinen:
- Lungenschäden durch das Einatmen von Schadstoffen (teilweise krebserregend)
- Brand- und Explosionsgefahr durch Funken und hohe Arbeitstemperaturen
- Blend- und Verbrennungsgefahr durch helles Licht des Plasmaschneiders
Um das Risiko von Unfällen und Verletzungen auf ein Minimum zu reduzieren, sind eine Reihe von Schutzmaßnahmen zu ergreifen. Die folgende Übersicht fasst die wichtigsten zusammen:
- Schutzbrille tragen, um die Augen vor Licht und Partikeln zu schützen
- Atemschutzmaske tragen, um keine schädlichen Stoffe einzuatmen
- lange Kleidung tragen (z. B. feuerfest), um die Haut vor Verbrennungen zu schützen
- Ohrenschützer tragen, um das Gehör vor lauten Arbeitsgeräuschen zu schützen
- Schutzhandschuhe tragen, um die Hände vor Verbrennungen zu schützen
- brennbaren Materialien mind. 10 m entfernt lagern, um Brände zu vermeiden
- Feuerlöscher bereithalten, um bei Bränden schnell eingreifen zu können
Wichtig ist es darüber hinaus, Plasmaschneider im besten Falle nur draußen zu verwenden und die Werkstücke vor dem Beginn der Arbeiten zu reinigen. Letzteres reduziert die entstehenden Schadstoffe und sorgt damit für bessere Luftverhältnisse am Arbeitsbereich.
FAQ: Am häufigsten gestellte Fragen zum Plasmaschneiden
Was ist Plasmaschneiden und wie funktioniert es?
Das Plasmaschneiden ist ein thermisches Trennverfahren. Es setzt auf einen heißen und beschleunigten Plasmastrahl (ionisiertes, elektrisch leitfähiges Gas), der Werkstoffe mit einer Temperatur von bis zu 30.000 Grad Celsius schmelzt und austreibt. Das Verfahren kommt ohne chemische Reaktion aus, setzt aber elektrischen Strom voraus, um einen energiereichen Lichtbogen auszubilden.
Welche Voraussetzungen gibt es und wann kommen Plasmaschneider zum Einsatz?
Voraussetzung ist, dass die zu bearbeitenden Materialien elektrisch leitfähig sind. Das ist bei Metallen wie unlegierten und hochlegierten Stählen der Fall. Bearbeiten lassen sich damit unter anderem Baustahl, Edelstahl, Aluminium, Messing oder Kupfer. Zum Einsatz kommen Plasmaschneider dabei gleichermaßen in Hobby- und Fachwerkstätten wie auch in industriellen Fertigungsanlagen. Unterscheiden lassen sich dabei Handgeräte und mechanisierte Plasmaschneider.
Was sind Vor- und Nachteile des Plasmaschneidens?
Von Vorteil ist der sehr große Einsatzbereich (alle elektr. Leitfähigen Materialien). Das Plasmaschneiden funktioniert außerdem schnell sowie präzise und der Wärmeeintrag in das zu bearbeitende Material ist gering (wenig Verzug etc.). Nachteilig sind die Einsatzgrenzen (Blechstärke bis max. 180 mm je nach Verfahren und Material). Die Schnittfuge ist eher breit und das Verfahren durch den hohen Stromverbrauch kostenintensiver als andere.
Welche Gase benötige ich zum Plasmaschneiden?
Je nach Verfahren benötigen Sie zum Plasmaschneiden Zündgase (Zündung, Pilotlichtbogen), Schneidgase (Arbeitsgas) und Sekundärgase (Düsenkühlung, Lichtbogeneinschnürung und Schmelzaustrieb). Als Arbeitsgase kommen dabei Druckluft (unlegierter Stahl, legierte Stahl, Aluminium), Stickstoff (N, rostfreier Stahl und Nichteisen-Metalle), Sauerstoff (O₂, unlegierter Stahl), Argon (Ar, im Gemisch, als Zünd- oder Sekundärgas), Wasserstoff (H2, im Gemisch oder als Sekundärgas), Argon-Wasserstoff-Gemische (legierten Stahl und Aluminium) und Stickstoff-Wasserstoff-Gemische (hochlegierte Stähle und Aluminium) zum Einsatz.
Welche Sicherheitsmaßnahmen sind zu beachten?
Wichtig ist das Tragen geeigneter Schutzkleidung. Dazu gehören lange Sachen (am besten feuerfest), Schutzbrillen und Schutzhandschuhe. Außerdem empfiehlt sich das Tragen einer Atemschutzmaske und eines Gehörschutzes. Brennbare Materialien sollten sich nicht in der Nähe des Arbeitsbereiches befinden und ein Feuerlöscher sollte griffbereit sein.