Additive Fertigung beschreibt Verfahren, bei denen durch schichtweisen Auftrag von Materialien dreidimensionale Werkstücke produziert werden. Selektives Laserschmelzen gehört zu diesen Verfahren. Im Vergleich zum Lasersintern ist hier der Ausgangswerkstoff zumeist ein Metallpulver, das in Schichten mittels Pulverbettverfahren aufgeschmolzen wird. Die Form der zu fertigenden Bauteile entspricht Vorlagen einer CAD-Programmierung.
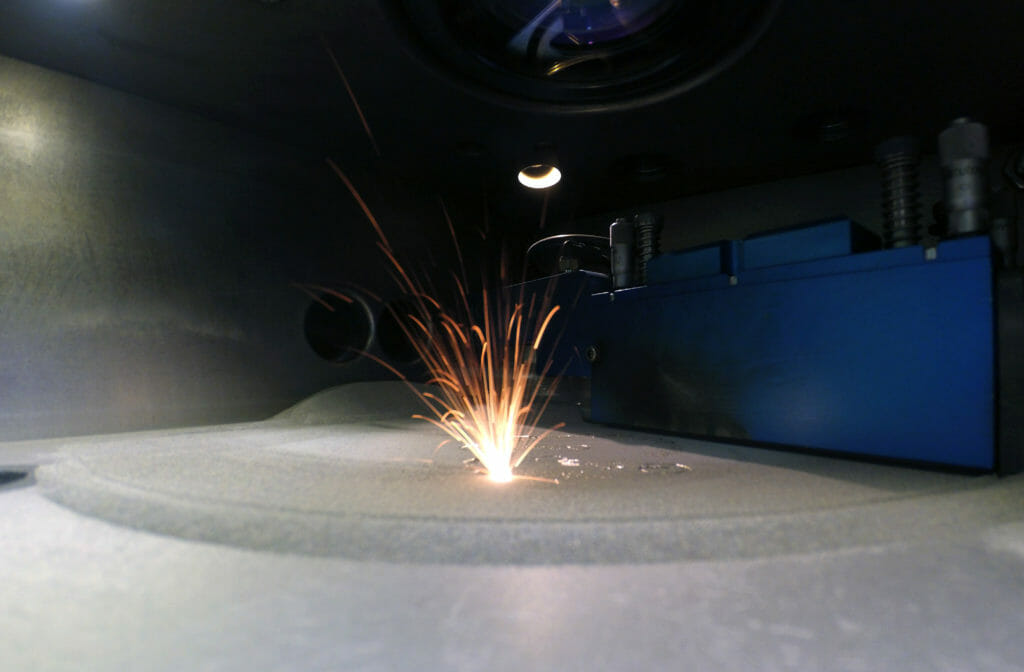
Das Ergebnis beim 3D Metalldruck sind einzelne Prototypen für Tests oder Endbauteile in geringer Stückzahl. Die so gedruckten Bauteile stehen traditionell gefertigten Teilen in Sachen Belastbarkeit wenig oder nichts nach. Sie können bei Bedarf relativ einfach und schnell nachbearbeitet werden und fügen sich in die Funktionalität eines Endprodukts optimal ein.
3D Metalldruck – Funktionsweise
Verfahren der Powder-Bed-Fusion-Technologie (PBF) mit Metallpulver wurden in den 1990er Jahren entwickelt. Neben dem DMLS (Direct Metal Laser Sintering) wurde 1995 das Selective Laser Melting patentiert und seitdem weiterentwickelt. Es handelt sich beim SLM um ein Schmelzverfahren, im Gegensatz zum “Sintern”, wo die Ausgangsstoffe erhitzt und verbunden werden, aber nicht komplett verschmelzen! Das ermöglicht eine deutlich bessere Dichte und Stärke der Materialien.
Ausgangspunkt des Verfahren sind 3D-CAD Modelle, die wiederum in einzelne Schichten aufgeteilt werden. In einem 3D-Metalldrucker wird unter Zugabe von Schutzgas (Argon oder Stickstoff, abhängig vom Metall) dann Schicht für Schicht das gewünschte Metallpulver aufgetragen. Die Schutzgasatmosphäre verhindert dabei ein unerwünschtes oxidieren der beteiligten Werkstoffe. Ein Laser schmilzt die jeweils aufgetragene Pulverschicht bei Tempertaturen bis 1250°C, danach wird eine weitere Schicht Pulver aufgetragen und geschmolzen. Durch die großen Temperaturunterschiede zwischen der jeweils obersten Schicht und den bereits deutlich kühleren Schichten darunter kann es bei falscher Anwendung zu einem Verzug des Werkstücks oder einem Hochbiegen der Werkstückkanten kommen. Um das zu vermeiden müssen die Bauteile gegebenenfalls mittels einer Stützstruktur mit der Grundplatte verschweißt werden. Dieser Zusatz muss nach Abschluss der Fertigung manuell entfernt werden.
Unterschied des selektiven Laserschmelzens zu selektivem Lasersintern
Die Vorgehensweise beim selektiven Lasersintern ist ähnlich wie beim selektiven Laserschmelzen. Während beim Sintern vorwiegend mit Kunststoffpulver als Ausgangsmaterial gearbeitet wird, wird beim Schmelzen zumeist Metallpulver verwendet. Beim Sintern werden die beteiligten Grundwerkstoffe nicht vollständig geschmolzen, sie bleiben üblicherweise unter ihrem jeweiligen Schmelzpunkt. Zwar haben auch gesinterte Werkstücke eine belastbare Dichte, sind aber von ihrer Festigkeit nicht vergleichbar mit vollständig aufgeschmolzenen Teilen der Modelle beim 3D Metalldruck.
Technische Verwendungsmöglichkeiten für Werkstücke aus dem 3D Metalldrucker
Anwender für den 3D Metalldruck sind üblicherweise Branchen und Anwendungen, bei denen die Bauteile zwar in geringen Mengen hergestellt, gleichzeitig aber hohen materiellen Ansprüchen genügen müssen. Ab einer gewissen Stückzahl sind in der Regel Designs, die mit herkömmlichen Produktionsverfahren ihrer Bauteile funktionieren, deutlich wirtschaftlicher. Üblicherweise geht man ab einer Stückzahl von etwa 100.000 Stück pro Jahr davon aus, dass die klassischen Herstellungsverfahren deutlich günstiger als DMLS oder SLM Verfahren sind. Bei geringeren Mengen sollte man abhängig vom Mehrwert des möglicherweise besseren Designs auch die additiven Fertigungsverfahren in Betracht ziehen.
Verwendungsmöglichkeiten der additiven Werkstücke:
- Überall dort, wo in kürzester Zeit funktionsfähige Prototypen hergestellt werden müssen, deren Bauteile nicht in Serie hergestellt werden oder aufgrund ihrer komplexen Geometrie nicht hergestellt werden können.
- Projektbegleitende, schnelle Fertigung von Formen und Designelementen. So lassen sich gegebenenfalls direkt am Produkt haptische Probleme mit dem Design erkennen, die am Computermodell nicht ersichtlich waren. Änderungen am Modell lassen sich relativ einfach am 3D-Modell vollziehen und kostengünstig neu erstellen lassen, bevor die Produktion in Serie geht.
Mögliche Metalle bzw. Metalllegierungen zum Laserschmelzen
- Aluminium AlSi10mg
- Edelstahl 1.4404 und 1.4542
- Werkzeugstahl 1.2709
- Inconel 718 (Nickelbasislegierung 2.4668)
- Kupfer CuNi2SiCr
- Cobalt-Chrom
- Titan Ti6Al4V
Einsatzmöglichkeiten des selektiven Laserschmelzen
In Zeiten immer neuer Herstellungsmöglichkeiten vervielfältigen sich auch deren Anwendungen in der technischen Realität. Vor allem in den folgenden Branchen (beispielhafte Aufzählung) gehört selektives Laserschmelzen längst zum entwicklerischen und produktiven Alltag.
Automobilindustrie
Aufgrund der hohen Kosten und eher geringen Stückzahlen spielt das pulverbettbasierte Laserschmelzen in der automobilen Massenfertigung (noch) keine große Rolle. Vor allem bezüglich der Größe sind hier Grenzen gesetzt, außerdem sind die so gefertigten Bauteile aufgrund ihrer Oberflächenbeschaffenheit nur bedingt für außen liegende Teile geeignet.
Im Motorsport findet die additive Fertigung allerdings schon heute Anwendung. Mit Hilfe des 3D Metalldrucks können kleinste und komplexe Bauteile innerhalb weniger Stunden produziert werden. So können Prototypen zügig entwickelt und bei Bedarf schnell angepasst werden. Durch die enorme Zeitersparnis der additiven Fertigung sinken letztendlich die Teilekosten, da keinerlei bestehenden Produktionsprozesse umgestellt und neu kalibriert werden müssen. Die große Anzahl von metallischen und kunststoffbasierten Werkstoffen bietet zusätzlich großen gestalterischen Freiraum.
Werkzeug- und Maschinenbau
Hier spielt der 3D Metalldruck gleich mehrere Rollen. Einmal können damit Maschinenkomponenten für komplexe Aufbauten als Einzelstücke oder in Kleinserien hergestellt werden. Zum Anderen lassen sich für die spätere Montage, Wartung und Reparatur selbst komplizierter Einzelformen die millimetergenau passenden Werkzeuge für das jeweilige Werkstück über selektives Laserschmelzen gleich mit produzieren. Dies kann wichtig sein, wenn es sich bei den entwickelten Maschinen um Spezialkonstruktionen handelt. Für solche Innovationen sind sehr oft Werkzeuge im Handel noch gar nicht entwickelt, da ja das entsprechende Modell für den Markt noch unbekannt ist. Inzwischen gängige Bereiche im Werkzeug- und Maschinenbau sind der Formenbau und Spezialausrüstung für Spritzgießprozesse.
Kreative Design- und Schmuckhersteller
Schmuckherstellung ist ein kreatives Gebiet ohne gedankliche Grenzen. Grenzen setzen nur die verwendeten Materialien und die Komplexität der erdachten Formen. Selektives Laserschmelzen macht gewagte Neukreationen möglich. Schon immer bestand das Designziel in der Schmuckentwicklung darin, so filigran wie möglich zu arbeiten. Durch 3D Metalldruck lassen sich selbst solche Formen umsetzen, die mit Feinwerkzeug nicht zu bearbeiten wären. Ein Vorteil für die in dieser Branche verwendeten Materialien ist die Möglichkeit, mit exakt programmierten Schmelztemperaturen zu arbeiten. Denn Edelmetalle haben sehr unterschiedliche Schmelztemperaturen, die bei Über- oder Unterschreitung die Versuche zunichte machen würden. Bei der SLM-Technologie kann ein solches Risiko ausgeschlossen werden.
Luft- und Raumfahrt
Entwicklungen in der Luft- und Raumfahrt sind ein Projekt von mehreren Jahren, teilweise Jahrzehnten. Vor allem für Raumfahrtpläne müssen Bauteile Extrembedingungen standhalten. Ein Test am Zielort ist aber aus Kostengründen und aufgrund der extremen Entfernungen nicht möglich. Also kommt es darauf an, auf der Erde Testumgebungen zu simulieren. Dabei ist ein Verlust an entwickelten Bauteilen unausweichlich. Jedoch können über das Wechselspiel Idee – Entwicklung – Test sehr schnell Schwachpunkte korrigiert werden. Beispiele für erfolgreiche technische Innovationen sind Sonden und Mars-Rover. Für ihren Bau wurden manche Komponenten im 3D Metalldruck hergestellt. Als Ergebnis häufiger vergeblicher und endlich erfolgreicher Erd-Tests sind die jeweiligen Techniken jetzt auf ihren Missionen, und das in voll funktionstüchtigem Zustand. Weitere Anwendung soll die additive Fertigung metallischer Werkstoffe und Komponenten auf kurz oder lang auch während Weltraummissionen im All finden. Werkzeuge und Ersatzteile ließen sich dann in den Raumstationen herstellen, die Herstellung auf der Erde und der komplizierte Transport ins All würden so entfallen.
Medizintechnik
Die nötigen Einzelteile in der Medizin sind so individuell wie jeder Patient. Über selektives Laserschmelzen können Implantate und anderer Zahnersatz als Einzelanfertigungen entstehen. Orthopädische Verwendungen sind künstliche Gelenke für Hüfte oder Knie. Selbst als Stützelemente für die Wirbelsäule können anatomisch exakt angepasste Teile über den 3D Metalldruck gefertigt werden. Der Aspekt Individualität ist wichtig. Noch essenzieller für den Nutzen der SLM-Technologie ist die nötige Zeit zwischen CAD-Modellentwicklung und Einsatzbereitschaft für notwendige Behandlungen. Oft müssen Gelenke lebensrettend sehr schnell ersetzt werden. Selektives Laserschmelzen verkürzt ansonsten lange Wartezeiten deutlich. Ebenfalls sind Zeiten zwischen dem Nehmen eines Zahnabdrucks und der Nachbildung im zahnmedizinischen Labor erheblich kürzer. Auch der geringe Verlust an verwendetem Material ist erwähnenswert.
3D Metalldruck – Vor- und Nachteile im Überblick
Selektives Laserschmelzen wird, ähnlich wie die meisten anderen additiven Fertigungsverfahren, zukünftig eine noch bedeutendere Rolle spielen. In der Anschaffung und im Betrieb sind die Initialkosten dieses Verfahrens noch relativ hoch. Entsprechende 3D Drucker sind noch relativ teuer und die verwendeten Metallpulver auch nicht unbedingt günstig. Im richtigen Anwendungsfall bietet die Einführung der SLM-Technologie langfristig allerdings viele Vorteile, denen vergleichsweise wenige Nachteile gegenüberstehen.
Hier sind die wichtigsten Vor- und Nachteile nochmals zusammengefasst:
Vorteile
- Die Eigenschaften des Ausgangsmaterials bleiben auch nach dem Aufschmelzen weitestgehend erhalten. Dadurch ergibt sich eine besondere Festigkeit der Bauteile, die sich so dann auch direkt in den jeweiligen Anwendungen verwenden lassen.
- Die Produktionszeit komplexer geometrischen Formen verringert sich immens, in hochtechnologischen Anwendungen mit kleinen Stückzahlen ist das Verfahren sehr zeitsparend und heutzutage schon nahezu konkurrenzlos.
- Die Zeiträume zwischen Planung und versuchsfähigen Prototypen verkürzt sich enorm, gleichzeitig lassen sich Änderungen am Design sehr schnell umsetzen. Das ermöglicht eine sehr praxisorientierte Entwicklung.
- Selektives Laserschmelzen ist eine moderne Variante solcher Bearbeitungsmethoden wie Drehen oder Fräsen. Bei diesen herkömmlichen Bearbeitungen fallen Metallspäne als Abfall an. Beim 3D Metalldruck steht grundsätzlich auch mehr Metallpulver als notwendig zur Verfügung. Allerdings kann der Pulverrest sofort für weitere Werkstücke verarbeitet werden.
- Die Anwendungsmöglichkeiten des 3D Metalldrucks sind nicht auf Prototypen und Test-Werkstücke oder Unikate begrenzt. So lassen sich teilweise Werkstoffe auf bereits vorhandene Objekte aufdrucken und bieten somit neue Gestaltungsmöglichkeiten.
- Aus den genannten Vorteilen entsteht eine weitere positive Tendenz: Kostenersparnis. Weniger Abfall bedeutet mehr Werkstücke aus dem jeweils gekauften Rohstoff. Die Entwicklungszeiten für Prototypen sinkt enorm und geht möglicherweise mit einer schnelleren Markteinführung damit einer schnelleren Amortisation der einmal getätigten Investition einher.
Nachteile
- Im Gegensatz zu herkömmlichen Herstellungsmethoden ist das Laserschmelzen relativ langsam, was die Herstellung großer Stückzahlen unwirtschaftlich macht.
- Die Technik ist nicht günstig und entsprechende 3D-Metalldrucker sind kostspielig in der Anschaffung. Einige Anbieter nutzen die angeschafften 3D Metalldrucker zur Ausführung externer Aufträge. Deren Kosten für die Anschaffung und Wartung der Technik splitten sich auf die verschiedenen Kunden und sind so letztendlich für alle günstiger.
- Für funktionsfähige Ergebnisse benötigt selektives Laserschmelzen enorme Temperaturen von bis zu vierstelligen Grad-Celsius-Werten. Für den Energieverbrauch kleiner Unternehmen bedeutet das hohe Kosten bei jeder Anwendung.
- In der möglichen Herstellungsgröße sind SLM-Druckobjekte vorläufig nach oben begrenzt. In speziellen Fällen müssen Werkstücke in mehreren Komponenten gedruckt und anschließend durch Nacharbeit miteinander verbunden werden. Allerdings arbeiten die Entwicklung fieberhaft an bezahlbaren Lösungen, die selbst so gewaltige Bauteile wie Karosseriestücke für Flugzeuge herstellen können. Für künftige Leichtbauweisen ist diese Aussicht positiv.
Fazit und Ausblick
Wie viele andere additive Fertigungsverfahren auch, ist selektives Laserschmelzen eine Technologie mit enormem Zukunftspotenzial. Schon heute bedienen sich viele, vor allem hochtechnologische Anwendungen und Industriezweige dieser Technologie.
Für die Massenproduktion ist das selektive Laserschmelzen zur Zeit noch nicht geeignet, dafür sind die Kosten pro Stück noch zu hoch und die Herstellungszeiten zu langwierig. Gleichzeitig ist auch die Maximalgröße der Bauteile bei derzeitiger Technik noch begrenzt.
Die Nachteile von relativ hohen Kosten und einer langsameren Produktionsgeschwindigkeit werden vor allem in der Entwicklung von Prototypen und der geringen Zeit zwischen Entwicklung einer CAD-Vorlage und dem fertigen Bauteil im 3D Metalldruck kompensiert. Bei der Herstellung kleiner Stückzahlen und gleichzeitig komplexen Geometrien der Bauteile ist das Verfahren schon heute rentabel und nahezu konkurrenzlos.
Vor allem die mögliche Komplexität der Bauteile ohne kritisches Zusammensetzen einzelner Komponenten schafft Werkstücke mit geringerem Verschleiß, hoher Belastbarkeit und neuartiger Funktionalität. Die Zukunft von SLM und DMSL-Verfahren ist jedenfalls sehr spannend zu verfolgen.