Sind Sie auf der Suche nach einem leistungsfähigen sowie genauen Trennverfahren, das für nahezu alle Materialien infrage kommt? Dann ist das Laserschneiden eine interessante Lösung. Zum Einsatz kommt dabei ein energiereicher Laserstrahl, der punktgenau auf das zu bearbeitende Werkstück trifft. Das Material schmilzt oder verdampft dabei und es entsteht eine saubere, sehr feine Schnittkante mit hoher Qualität. Wie das funktioniert, welches Zubehör erforderlich ist und warum die Kühlung beim Laserschneiden eine große Rolle spielt, erklärt gasido.de im folgenden Beitrag.
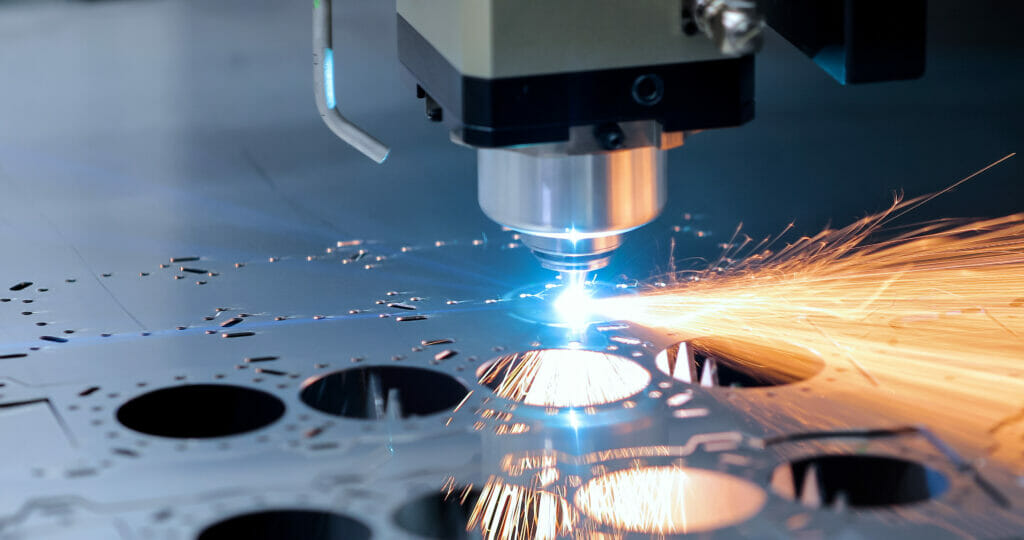
Themen im Überblick
- Wie funktioniert das Laserschneiden? Der Prozess verständlich erklärt
- Laser trennen nahezu alle Materialien: Einsatzbereiche und Vorteile
- Varianten des Laserschneidens und Bauarten der Laser im Vergleich
- Wichtige Einflussfaktoren für Qualität und Leistung beim Laserschneiden
- Die richtigen Gase für den Laser: Das zu trennende Material entscheidet
- Effektive Kühlung für Leistung und Lebensdauer beim Laserschneiden
- Übliche Preise und Kosten der Laser zum Laserschneiden im Überblick
- FAQ: Häufig gestellte Fragen und verständliche Antworten zum Thema
Wie funktioniert das Laserschneiden? Der Prozess verständlich erklärt
Was sich nach Zukunftstechnologie anhört, ist in der Industrie bereits weit verbreitet und mit vielen Vorteilen verbunden. Die Rede ist vom Laserschneiden, bei dem ein hochenergetischer Laserstrahl konzentriert auf die Oberfläche der zu trennenden Materialien trifft. Ist die punktgenau eingebrachte Hitze dabei so groß, dass sie nicht mehr ausreichend abströmen kann, beginnt das Trennverfahren und die zu bearbeitenden Materialien schmelzen, verbrennen oder verdampfen. Ein zusätzlicher Gasstrahl spült die abgetragenen Stoffe aus der Schnittlinie und sorgt somit für einen sauberen sowie schnellen Schneidprozess.
Übrigens:
Der Begriff „Laser“ wurde schon 1958 vom amerikanischen Physiker und Ingenieur Theodore H. Maiman eingeführt. Er beschreibt die Lichtverstärkung durch stimulierte Emission von Strahlung.
Verschiedene Komponenten ermöglichen das Trennen mit einem Laserstrahl
Damit der oben beschriebene Prozess funktioniert, sind verschiedene Bauteile erforderlich. Die folgende Übersicht zeigt, was diese auszeichnet:
- Laserstrahlquelle: Die Laserstrahlquelle erzeugt einen Lichtstrahl mit hohem Energieinhalt, der beim Laserschneiden zum Trennen von Materialien erforderlich ist. Bei Feststofflasern wie dem Nd:YAG-Laser funktioniert das beispielsweise, indem das Licht einer Lichtquelle durch eine Linse gebündelt auf einen speziellen Kristall trifft. Paarweise angeordnete Spiegel (auch Resonator) reflektieren es hier so lange, bis das gesamte Licht in eine Richtung scheint und durch einen teilweise durchlässigen Spiegel austritt.
- Laserstrahlführung: Die Laserstrahlführung leitet den Strahl von seiner Quelle ab. Abhängig von der Art des Lasers funktioniert das mit Glasfasern (Lichtleitkabeln) oder Umlenkspiegeln. Während ersteres bei Feststoff- (Nd:YAG-), Faser- und Scheibenlasern zum Einsatz kommt, setzen CO2-Laser Umlenkspiegel voraus.
- Fokussieroptik: Das nächste Bauteil des Laserstrahls ist die Fokussieroptik an der Bearbeitungsstelle. Diese bündelt den Laserstrahl so, dass sein Fokus, also der Bereich mit dem höchsten Energieinhalt, genau auf die zu bearbeitende Stelle trifft. Das ist wichtig, um die zum Laserschneiden erforderliche Intensität zu erreichen.
- Schneiddüse: Durch die Düse treten Laserstrahl und Schneidgas aus dem Laser aus. Sie treffen auf das zu bearbeitende Werkstück, erhitzen dieses punktuell und führen so zum Schmelzen, Verbrennen oder Verdampfen. Der mit dem Laserstrahl austretende Schneidgasstrahl spült die Materialreste weg und hinterlässt eine saubere, nahezu gradfreie Schnittkante.
Für eine hohe Qualität beim Laserschneiden ist es wichtig, dass alle Komponenten perfekt aufeinander und auf das zu bearbeitende Werkstück eingestellt sind. Das betrifft die Laserleistung genauso wie die Fokussieroptik und den Einsatz reiner Gase.
Laser trennen nahezu alle Materialien: Einsatzbereiche und Vorteile
Das Laserschneiden kommt heute für nahezu alle denkbaren Materialien infrage. Angefangen von einfachem Baustahl, über Edelstahl bis hin zu hoch reflektierenden Stoffen gibt es kaum Einschränkungen. Selbst dreidimensionale Bauteile, Textilien oder Glasplatten lassen sich mit dem Verfahren schnell, sauber und berührungslos trennen. Und nicht nur das. Denn im gleichen Arbeitsgang ist es oft auch möglich, Oberflächen zu gravieren.
Die wichtigsten Vor- und Nachteile des Laserschneidens im Vergleich
Durch den hohen Automatisierungsgrad und die berührungslose, sowie sehr genaue Bearbeitung ist das Schneiden mit Laserstrahlen mit vielen Vorteilen verbunden. Einer der wichtigsten ist der sinnvolle Einsatz, selbst bei kleinsten Stückzahlen. Das Verfahren besticht mit einer sehr hohen Flexibilität und sauberen, schmalen sowie nachbearbeitungsfreien Schnittkanten. Die Toleranzen sind minimal (+/- 0,1 mm/m) und die Schneidgeschwindigkeiten hoch (bis zu 250 m/min).
Nachteilig sind die hohen Anschaffungskosten. Das Verfahren benötigt viel elektrische Energie und stellt eine gewisse Gefahr für Anwender und Umwelt dar. So können gesundheitsgefährdende Gase sowie Aerosole entstehen. Außerdem ist es möglich, dass das eventuell ausgetretene Strahlung zu nicht gleich erkennbaren Augenschäden führt.
Die folgende Tabelle zeigt die wichtigsten Vor- und Nachteile des Laserschneidens im Vergleich:
Vorteile | Nachteile |
---|---|
Flexibilität | Anschaffungskosten |
Genauigkeit | Stromverbrauch |
nahezu keine Einsatzgrenzen | Schneidgasverbrauch |
feine Bearbeitung | Gefahren für Anwender und Umwelt |
saubere, schmale sowie nachbearbeitungsfreie Schnittkanten | |
geringe Toleranzen (+/- 0,1 mm/m) | |
hohe Schneidgeschwindigkeiten (250 m/min) | |
gravieren und trennen, oft in einem Arbeitsgang |
Wichtig zu wissen ist, dass Abluftanlagen und geschlossene Bearbeitungskabinen die Gefahren des Laserschneidens reduzieren. Besonders gut funktioniert das mit aktiven Kabinen, die den Laser abschalten, wenn sie fehlgeleitete Strahlung erkennen.
Varianten des Laserschneidens und Bauarten der Laser im Vergleich
Abhängig von den Eigenschaften der zu bearbeitenden Materialien unterscheiden Experten verschiedene Arten des Laserschneidens. Welche das sind und was diese auszeichnet, zeigt die folgende Übersicht:
- Schmelzschneiden: Bei diesem Verfahren schmelzen Laserschneidgeräte das zu bearbeitende Material, bevor sie die Schmelze mit einem inerten Gas ausblasen. Letzteres verhindert zudem die Oxidation des Werkstoffs. Es schützt den Laser bzw. die Fokussieroptik vor äußeren Einflüssen und sorgt für eine saubere Schnittkante. Infrage kommt das Laserstrahlschmelzschneiden, wenn es um die Bearbeitung von Edelstahl oder Aluminiumlegierungen geht.
- Brennschneiden: Kommt das Laserstrahlbrennschneiden zum Einsatz, erhitzt der Laser das zu bearbeitende Material auf Entzündungstemperatur. Parallel dazu bringt er Sauerstoff ein, der zum Verbrennen des Werkstoffs führt. Von Vorteil ist die sehr hohe Arbeitsgeschwindigkeit. Außerdem ist die Qualität durch nahezu gratfreie Schnittkanten sehr hoch. Infrage kommt die Art des Laserschneidens üblicherweise bei eisenhaltigen Metallen.
- Sublimierschneiden: Sublimiert ein Stoff, geht er vom festen direkt in den gasförmigen Aggregatzustand über. Genau das passiert auch beim Laserstrahlsublimierschneiden, wenn der energiereiche Laserstrahl Oberflächen stark erhitzt. Interessant ist das Verfahren für alle Werkstoffe, die nicht schmelzen. Beispiele dafür sind Holz, Leder, Stoffe oder faserverstärkte Kunststoffe.
Neben den hier vorgestellten Verfahren zum Laserschneiden gibt es auch das sogenannte Feinschneiden, das die Bearbeitung filigraner Teile ohne Wärmeverzug ermöglicht. Damit das funktioniert, arbeitet der Laser nicht kontinuierlich. Er flackert (pulsiert) und setzt dabei unzählige kleine Bohrungen, die sich teilweise überlappen. Die hohe und konzentrierte Energiedichte verhindert dabei, dass sich die Werkstücke stark aufheizen und dadurch verziehen.
Festkörper-, Gas- oder Faserlaser: Wann welcher Laser zum Einsatz kommt
Genau wie die Bearbeitungsverfahren lassen sich auch Laserbauarten unterscheiden. Geht es um das Laserschneiden, kommen dabei vor allem die Folgenden zum Einsatz:
- Festkörperlaser: Arbeiten Laser mit einem Festkörper, regen Lichtquellen (optische Pumpen wie Blitzlampen oder Dioden) Gläser oder spezielle Kristalle an, um den energiereichen Strahl zu erzeugen. Typische Beispiele sind der Nd:YAG-Laser, der Rubinlaser und der Ti:Saphir-Laser. Der Nd:YAG-Laser kommt dabei auch beim Laserschneiden zum Einsatz, wobei er sich für die Bearbeitung von Metallen, Kunststoffen sowie Keramik eignet. Nachteilig ist, dass Laserdioden sowie Kristalle kostspielig sind und eine vergleichsweise geringe Lebensdauer (8.000 bis 15.000 Stunden) aufweisen.
- Faserlaser: Anstelle von Feststoffen wie Gläsern oder Kristallen regen optische Pumpen hier Fasern als aktive Medien an. Die Laser sind vergleichsweise robust und liefern auch bei hoher Leistung eine optimale Strahlenqualität. Von Vorteil ist der hohe Wirkungsgrad, der zu geringeren Betriebskosten beim Laserschneiden führt. Faserlaser sind zudem kompakt und wartungsfreundlich. Sie benötigen kein Gas zur Übertragung des Laserstrahls und eignen sich für Metalle, die sie schnell schneiden oder gravieren. Letzteres gilt selbst für Messing und Kupfer. Für nichtmetallische Werkstoffe eignen sie sich hingegen nicht.
- Gaslaser: Bei Gaslasern stellt ein Gas das aktive Medium dar, welches elektrisch oder von anderen Lasern angeregt wird. Beispiele sind CO2-Laser und Argon-Ionen-Laser, wobei vor allem erstere häufig beim Laserschneiden zum Einsatz kommen. Sie eignen sich vor allem für nicht-metallische Materialien (Kunststoffe, Textilien, Holz etc.) und besitzen eine sehr hohe Strahlqualität.
Neben den hier beschriebenen Bauarten, die sehr häufig beim Laserschneiden zum Einsatz kommen, gibt es zahlreiche weitere. So zum Beispiel Farblaser, Halbleiterlaser, Freie-Elektronen-Laser (FEL), Chemische Sauerstoffjod-Laser (COIL), die sich für verschiedene andere Anwendungen eignen.
Übrigens:
Geht es um das Laserschneiden, sind die erprobten CO2-Laser heute weit verbreitet. Die noch jungen Faserlaser können durch ihre speziellen Eigenschaften und Vorteile in puncto Energieeffizienz und Wartungsfreundlichkeit jedoch aufholen. Entscheidend für die Auswahl eines Lasers sind aber nach wie vor die zu bearbeitenden Materialien. Geht es um Metalle, spielen Faserlaser ihre Vorteile voll aus. Bei nichtmetallischen Werkstoffen sind CO2-Laser hingegen häufig im Vorteil.
Wichtige Einflussfaktoren für Qualität und Leistung beim Laserschneiden
Wie in den vorherigen Abschnitten beschrieben, wirkt sich die Auswahl der richtigen Technik sehr stark auf die Qualität des Schneidvorgangs aus. Neben diesen kommt es aber auch auf die richtige Einstellung an.
Ein wichtiges Kriterium ist dabei der Fokus, dessen Lage und Durchmesser einen großen Einfluss auf die Bearbeitungsqualität haben. Die Einstellung wirkt sich auf die Leistungsdichte und die Form des Schnittspalts aus und ist jeweils individuell anzupassen. Ähnliches gilt für die Düse. Diese beeinflusst beim Laserschneiden die Gasmenge sowie die Form des Gasstrahls und ist passend zum Arbeitsgang auszuwählen.
Wichtig für eine geringe Rautiefe und Gratbildung ist darüber hinaus die Schneidgeschwindigkeit. Um optimale Ergebnisse zu erzielen, ist diese in Abhängigkeit von der Materialart, der Materialstärke und der Laserleistung auszuwählen. Dabei gilt: Je stärker das Material und je schwächer der Laser ist, umso langsamer sollte das Laserschneiden erfolgen.
Weitere Einflussfaktoren sind die Laserleistung, die Betriebsart (Dauerbetrieb oder pulsierend) sowie der Polarisationsgrad. Während die Laserleistung generell ausreichen muss, um den Werkstoff in der gewünschten Zeit entsprechend zu erhitzen, ist der Polarisationsgrad bei CO2-Lasern korrekt einzustellen. Letzteres ist wichtig, da sich das Schnittbild mit der Schnittrichtung ändert. Kommen Festkörper- oder Faserlaser zum Einsatz, spielt der Polarisationsgrad keine Rolle, da diese unabhängig von der Schneidrichtung immer mit der gleichen Qualität arbeiten.
Die richtigen Gase für den Laser: Das zu trennende Material entscheidet
Wie bei vielen Füge- und Trennverfahren ist auch das Laserschneiden nur mit technischen Gasen möglich. Welche dabei zum Einsatz kommen, hängt grundsätzlich von der Art des Laserschneidens, der Leistung des Lasers und von der individuellen Anwendung ab. Weit verbreitetet, sind Sauerstoff, Stickstoff und Argon. Darüber hinaus können Sie auch Helium sowie Kohlendioxid als Lasergas kaufen. Letzteres wird dabei als Resonatorgas im Laser selbst verwendet.
Qualität der technischen Gase beeinflusst die Qualität beim Laserschneiden
Wichtig zu wissen ist, dass Laserschneidgeräte hohe Anforderungen an die eingesetzten Gase stellen. Denn mit deren Reinheitsgrad verbessert sich die Schnittqualität und die mögliche Schneidgeschwindigkeit nimmt zu. Anstelle konventioneller technischer Gase sollten Sie daher Gase der Stufe 3.5 oder höher einsetzen, um gute Ergebnisse zu erzielen. Die folgende Übersicht zeigt, welche technischen Gase dabei grundsätzlich infrage kommen.
Technisches Gas | Reinheit | Einsatzbereich (Bsp.) |
---|---|---|
Druckluft (rein aufbereitet) | k. A. | Sublimierschneiden |
Helium 4.6 | 99,996 Prozent | Schmelzschneiden, Sublimierschneiden |
Kohlendioxid 4.5 | 99,995 Prozent | Resonatorgas im CO2-Laser |
Stickstoff 5.0 | 99,999 Prozent | Schmelzschneiden, Sublimierschneiden |
Sauerstoff 3.5 | 99,95 Prozent | Brennschneiden |
Argon | k. A. | Schmelzschneiden, Sublimierschneiden |
Abhängig vom Laser, vom Trennverfahren und vom zu bearbeitenden Material kommen häufig auch Mischgase zum Einsatz. Diese setzen sich aus den oben aufgeführten Stoffen zusammen und sind mit verschiedenen Bezeichnungen zu kaufen. Die folgende Tabelle gibt einen ersten Überblick.
Mischgas zum Laserschneiden kaufen | Zusammensetzung |
---|---|
Lasergas I | CO2: 4,5 %, N2: 13,5 %, He: 82,0 % |
Lasergas II | CO2: 5,0 %, N2: 55,0 %, He: 40,0 % |
Lasergas III | CO2: 3,4 %, N2: 15,6 %, He: 81,0 % |
Lasergas IV | CO2: 1,7 %, N2: 23,4 %, He: 74,9 % |
Lasergas V | CO2: 5,0 %, N2: 35,0 %, He: 60,0 % |
Lasergas VI | CO2: 4,0 %, N2: 35,0 %, He: 60,0 % |
Lasergas VII | CO2: 3,14 %, N2: 31,4 %, He: 65,46 % |
Lasergas VIII | CO2: 5,4 %, N2: 27,0 %, He: 67,6 % |
Die Angaben in der Tabelle beziehen sich auf die oben genannten Gasqualitäten und geben einen ersten Überblick. Verbindliche Informationen zur Zusammensetzung der Mischgase finden Sie in den Herstellerunterlagen Ihres Laserschneid-Geräts.
Übrigens:
Die Gase haben beim Laserschneiden gleich mehrere Funktionen. Während sie teilweise zum Verbrennen des Werkstoffs nötig sind, schützen sie dessen Oberfläche sowie den Schneidkopf vor Verunreinigungen. Sie spülen abgetragenes Material weg und entfernen die Plasmawolke über dem Werkstück. Häufig sollen die Gase das zu bearbeitende Material auch kühlen, um eine zu große Wärmeeinwirkung zu verhindern.
Mischgase kaufen oder Gase mit Mischanlage selbst bereitstellen
Grundsätzlich können Sie Gase zum Laserschneiden einzeln in Flaschen oder fertig als Mischgas kaufen. Letzteres ist vergleichsweise teuer und daher nur für kleinere Bedarfe erforderlich. Setzen Sie das Verfahren sehr häufig ein oder verwenden es für unterschiedliche Werkstoffe, empfehlen sich Gasmischanlagen. Diese stellen Mischgase bedarfsgerecht her und sorgen somit für eine hohe Flexibilität. Von Vorteil ist außerdem, dass die Gase in Reinform meist günstiger sind als fertig gemischt.
Die passende Lieferform der Gase zum Laserschneiden wählen
Geht es um die Lieferform, kommen grundsätzlich Gasflaschen, Gasflaschenbündel und Großtanks infrage. Erstere eignen sich für kleine Bedarfsmengen. Sie sind vergleichsweise teuer und aufwendiger im Handling.
Benötigen Sie mehr Gas und möchten Arbeit sowie Geld sparen, kommen Gasflaschenbündel zum Einsatz. Diese bestehen aus zwölf 50-Liter-Gasflaschen und lassen sich bei Bedarf zu Bündelbatterieanlagen zusammenschließen.
Decken auch diese nur einen kleinen Teil des eigenen Bedarfs, eignen sich Großtanks für tiefkalt verflüssigte Gase. Diese beinhalten bis zu 80.000 Liter Flüssigkeit, um abhängig von der Gasart 50.000 bis 60.000 Kubikmeter Gas zur Verfügung zu stellen. Möglich ist das mit Verdampfern, die ausreichend Wärme einbringen, um die Flüssigkeit ohne Vereisung in den gasförmigen Zustand zu überführen.
Übrigens:
Wie hoch beim Laserschneiden der Gasverbrauch ist, hängt neben dem Laser auch von der Einsatzdauer ab.
Auch beim Gasnetz für Laserschneidgeräte auf Qualität achten
Um beim Laserschneiden eine hohe Qualität sicherstellen zu können, kommt es nicht nur auf die Gase selbst an. Auch die Verrohrung in der Anlage hat dabei hohe Anforderungen zu erfüllen. Sie muss für reine Gase geeignet, sauber und fachgerecht verlegt worden sein. Infrage kommen dabei zum Beispiel fett- und ölfreie Kupferleitungen oder Kunststoffschläuche in hoher Qualität. Zudem sind Reinstgasarmaturen mit zweistufiger Druckreduzierung bzw. mit Metallmembrane aus Edelstahl zu empfehlen.
Effektive Kühlung für Leistung und Lebensdauer beim Laserschneiden
Nehmen Laser ihren Betrieb auf, entsteht eine erhebliche Wärmemenge, die teilweise zum Bearbeiten der Werkstoffe erforderlich ist. Im Laser selbst kann sich überschüssige Wärme jedoch nachteilig auswirken. So sind Ungenauigkeiten bei der Bearbeitung und sogar verzogene Bauteile möglich. Um das zu verhindern, setzen Hersteller vor allem bei Geräten mit größerer Leistung auf aktive Kühlsysteme. Diese leiten Kühlmedien unter stofflicher Trennung an den wichtigsten Komponenten der Laserschneid-Geräte vorbei, um Energie aufzunehmen und abzuführen.
Übrigens:
Als Wärmeträgermedium kommt beim Laserschneiden häufig Wasser (Trinkwasser oder deionisiertes Wasser) zum Einsatz. Möglich ist der Betrieb aber auch mit Wasser-Glykol-Gemischen (bei Frostgefahr), Ölen und anderen Medien.
Rückkühler und Kältemaschinen führen überschüssige Wärme ab
Hat sich das Wärmeträgermedium im Laser erwärmt, strömt es mit höherer Temperatur zu einem Rückkühler oder einem Kaltwassersatz. Während ersterer die Wärme ohne weiteren technischen Prozess an Luft oder Wasser überträgt, sorgen Kaltwassersätze mit einem Kälteprozess für punktgenaue Temperaturbedingungen.
Dazu kühlen sie das Wärmeträgermedium aus dem Lasert zunächst mit einem Kältemittel herunter. Dieses geht daraufhin in den gasförmigen Aggregatzustand über, bevor ein Verdichter mit dem Druck auch die Temperatur erhöht. Das ist die Voraussetzung dafür, dass das Medium im nächsten Schritt Wärme an die Umgebung abgeben kann. Es kühlt selbst ab, verflüssigt wieder und nimmt nach dem Durchströmen eines Expansionsventils seinen ursprünglichen Zustand wieder ein. An diesem Punkt beginnt der Vorgang von vorn, um die Wärme vom Laserschneiden dauerhaft abführen zu können.
Übliche Preise und Kosten der Laser zum Laserschneiden im Überblick
Wie viel das Laserschneiden kosten kann, lässt sich nicht pauschal beurteilen. Denn genau wie die Anschaffungskosten hängen auch die Betriebskosten sehr stark von den individuellen Gegebenheiten ab. Zu den wichtigsten Einflussfaktoren gehören dabei die Art des Lasers, die Leistung sowie die Art und der Verbrauch des Lasergases.
Gleiches gilt für die Lasergas-Kosten, die sich ebenfalls nicht pauschal angeben lassen. Wichtig zu wissen ist hier jedoch, dass kleine Liefer- und Bestellmengen in aller Regel mit höheren Preisen einhergehen.
Unser Tipp:
Lassen Sie sich individuell beraten, um die passende Technik für Ihre Anwendung(en) zu finden. Aufbauend auf einer individuellen Planung kalkulieren Anbieter daraufhin die Preise der Laserschneider. Zudem können Sie nach erfolgter Geräteauswahl bereits Gaslieferanten vergleichen und Angebot einholen.
Zuschnitte einkaufen oder Laserschneid-Anlage anschaffen: Was ist besser
Parallel zur Frage nach den Kosten des Laserschneidens geht es oft auch darum, für wen sich eine solche Anlage lohnt. Ein wichtiger Richtwert ist dabei der Betrag der jährlichen Kosten für den Einkauf bereits zugeschnittener Teile. Liegt dieser bei 50.000 bis 60.000 Euro, kann es sich lohnen, selbst einen Laserschneider zu kaufen. Die geringeren Ausgaben sorgen dabei in der Regel für so hohe Einsparungen, dass sich die Kosten innerhalb von 5 bis 7 Jahren amortisieren. Ob das auch für Ihren Fall gilt, zeigt die individuelle Kosten-Kalkulation von einem Anbieter oder Hersteller der Laserschneid-Maschinen.
FAQ: Häufig gestellte Fragen und verständliche Antworten zum Thema
Was ist das Laserschneiden und wie funktioniert die moderne Technik?
Das Laserschneiden ist ein Trennverfahren, bei dem ein energiereicher Laserstrahl auf die zu bearbeitende Oberfläche trifft. Er kann dauerhaft anliegen oder pulsieren, um die Materialien zu schmelzen, zu verbrennen oder zu verdampfen. Je nach Einstellung können die sehr genauen Geräte Oberflächen gravieren oder Werkstücke komplett trennen.
Welche Vorteile hat das Laserschneiden und wo liegen Nachteile?
Das Laserschneiden bietet eine hohe Flexibilität. Es lässt sich schon bei Kleinserien oder Prototypen sinnvoll einsetzen und ist sowohl im 2D- wie auch im 3D-Bereich sehr genau. Hinzu kommt die Tatsache, dass sich neben Metallen auch nahezu alle anderen Materialien bearbeiten lassen. Die Schnitte sind immer schmal. Die Anlagen arbeiten dabei sehr genau sowie schnell. Nachteilig sind die Anschaffungskosten, der Stromverbrauch sowie der Verbrauch an Schneidgas.
Welche Materialien lassen sich mit einem Laser trennen oder bearbeiten?
Hier gibt es kaum Einschränkungen. Je nach Verfahren und Laser bearbeiten die Anlagen unter anderem Metall, Holz, Pappe, Leder, Textilien, Glas, Keramik sowie homogene und faserverstärkte Kunststoffe.
Welche Arten des Laserschneidens lassen sich voneinander unterscheiden?
Zu unterscheiden sind im Wesentlichen die Verfahren des Schmelzens, des Brennschneidens und des Sublimierschneidens. Beim Schmelzen erhitzt der Strahl ein Werkstück so stark, dass das Material an der Schnittkante schmilzt und von den Lasergasen ausgespült wird. Beim Brennschneiden verbrennt das Material zusammen mit Sauerstoff direkt und beim Sublimierschneiden geht es vom festen in den gasförmigen Aggregatzustand über. Letzteres funktioniert zum Beispiel mit einem CO2-Laser beim Trennen von Leder oder Holz sowie anderen Materialien, die über keine ausgeprägte Schmelzphase verfügen. Für andere Verfahren eignen sich Feststofflaser wie Kristall (Nd:YAG-Laser) oder Faserlaser.
Wie lassen sich Leistung, Effizienz und Qualität beim Schneiden optimieren?
Für eine optimale Qualität und Effizienz kommt es auf die Auswahl passender Komponenten an. Wichtig ist darüber hinaus die bedarfsgerechte Konfiguration (Schnittgeschwindigkeit, Fokus, Düsengröße, Polarisation) der Laserschneidanlage. Nicht zuletzt spielt auch das eingesetzte Gas eine entscheidende Rolle. Ist es rein und in ausreichendem Druck verfügbar (Herstellerunterlagen beachten), wirkt sich das positiv auf die Schnittgeschwindigkeit und die Schneidqualität aus.
Welche Gase kommen beim Laserschneiden zum Einsatz?
Infrage kommen Druckluft, Helium 4.6, Kohlendioxid 4.5, Stickstoff 5.0, Sauerstoff 3.5 und Argon sowie Gemische aus den verschiedenen Gasen. Entscheidend für die Auswahl und Zusammensetzung sind dabei das Verfahren und das zu bearbeitende Werkstück. Hersteller helfen dabei, die individuell beste Gasmischung zu finden.
Warum ist die Kühlung der Laser wichtig und wie funktioniert sie?
Bei dem Betrieb der Laser entsteht viel Wärme, die Komponenten beschädigen und zu einem ungenauen Ergebnis beim Laserschneiden führen könnte. Um das zu verhindern, sind vor allem Laser mit höherer Leistung zuverlässig zu kühlen. Möglich ist das unter anderem mit Kaltwassersätzen, die ein Wärmeträgermedium (Wasser, Wasser-Glykol-Gemisch, deionisiertes Wasser, Öl etc.) zur Flüssigkeitskühlung auf die benötigte Temperatur bringen.
Wie viel kann Laserschneiden kosten und wann lohnt sich die Anschaffung?
Verbindliche Auskünfte zu den Kosten des Laserschneidens sind nicht möglich. Gleiches gilt für die Lasergas-Preise. Grund dafür sind unterschiedliche Ausführungen, Anwendungen und Ausstattungen, die zu großen Preisunterschieden führen. Wir empfehlen daher, eine passende Anlage vorauswählen und den individuellen Preis kalkulieren zu lassen, bevor Sie Lasergas bestellen. Lohnen kann sich die Anschaffung einer Anlage im industriellen Stil grundsätzlich dann, wenn Sie zugeschnittene Teile einkaufen und dafür ab 50.000 bis 60.000 Euro pro Jahr zahlen.